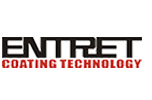
Vacuum coating application is a large branch of vacuum application, which has a very wide range of applications in many aspects such as optics, electronics, physical and chemical instruments, packaging, machinery and surface treatment technology. In order to give you a more detailed understanding of the application of vacuum coating, today the editor will introduce the main methods of vacuum coating for you in detail, I hope it will be useful to everyone!
The simple understanding of vacuum coating application is to coat metal films or coatings on metal, glass, ceramics, semiconductors and plastic parts in a vacuum environment using evaporation, sputtering and subsequent condensation. Compared with the traditional coating method, the vacuum coating application is a dry coating, and its main methods include the following:
Vacuum evaporation
The principle is to use an evaporator to heat the vaporized material to vaporize or sublime under vacuum conditions. The vaporized ion stream directly shoots to the substrate and deposits a solid thin film on the substrate.
Sputter coating
Sputtering coating is under vacuum conditions, the cathode is connected to a high voltage of 2000V to excite glow discharge, and the positively charged argon ions hit the cathode to eject atoms, and the sputtered atoms are deposited on the substrate through an inert atmosphere to form a film layer .
Ion plating
That is, the vacuum ion coating that the dry screw vacuum pump manufacturer has already introduced. It is developed on the basis of the above two vacuum coating technologies, so it has both process characteristics. Under vacuum conditions, gas discharge is used to separate the working gas or the evaporated material (membrane), and the evaporated material or its reactants are deposited on the surface of the substrate under ion bombardment. During the film formation process, the substrate is always bombarded by high-energy particles and is very clean.
Vacuum wound coating
Vacuum winding coating is a technology that uses physical vapor deposition to continuously coat a film on a flexible substrate to achieve some functional and decorative properties of the flexible substrate.
The above-mentioned four kinds are all belong to the application of physical vapor deposition technology (PVD).
Next is chemical vapor deposition (CVD). It uses a chemical reaction to make a thin film. The principle is that at a certain temperature, the reaction gas containing the film-forming material is passed to the substrate and is adsorbed, and a chemical reaction is generated on the substrate to form a nucleus, and then the reaction product is continuously separated from the surface of the substrate. Diffusion to form a thin film.
Beam deposition plating, combined with ion implantation and vapor deposition coating technology of ion surface composite treatment technology, is a technology that uses ionized particles as evaporation materials to form a thin film with good characteristics at a relatively low substrate temperature .